1) Not Understanding Your Target
An IR inspector cannot be an expert in everything but should at least be well informed about the potential problems that can be found during an inspection.
For example, if you are not a professional electrician, you must be aware of the typical thermal maps of each component that you want to inspect so you can recognize potential anomalies.
For example? Those solid-state diodes seem to show a loose connection, but they are absolutely normal. Luckily, the two similar components in the cabinet show the same thermal map, therefore, this tells the inspector that this is most likely the normal thermal behavior of this type of component (confirmed by the manufacturer).
But what if the cabinet contains only one component?
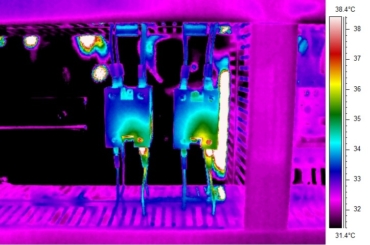
Two solid-state diodes seem to show a loose connection in the lower right cable: this is their typical thermal pattern.
Your mantra must be “learn.”
Never believe you are a super-expert: use your spare time to gain knowledge on how your possible targets work, which types of failure they could have and how those failures will appear during an IR survey.
2)Inspecting under the wrong conditions
Have you ever seen a museum when there wasn’t an exhibition in place? In a museum, lights and AC systems are the main electric loads. Without an exhibition, most electrical components won’t have enough load to be properly inspected. And without load, you will not be able to detect any electrical problem.
In an electrical circuit, the heat generation depends on the current crossing the circuit. In a mechanical system, it normally depends on dissipated power due to friction.
No power, no heat generation, means that a thermal anomaly cannot be detected. When possible, choose the best moment with the highest load. Or change your evaluation criteria to reflect a lower load than expected.
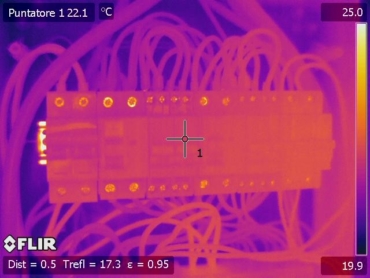
No load in this panel: all cases where the parts appear warmer are just due to the operator’s reflection on lower-emissivity surfaces, and the investigation is useless.
3)Using an IR camera of insufficient quality or taking images at the wrong distance
Today you can find very cheap IR cameras on the market. But what is the reason for the price difference between high-end and entry-level IR cameras (or mobile phone IR cameras)?
Here, the size matters. In terms of available pixels, obviously. You have probably never compared an IR camera to a digital camera. A digital camera has millions of pixels.
You don’t need a professional DSLR camera such as Canon, Nikon or Sony, which now have over 40 megapixels, to shoot a nice picture during your holiday. Even low-cost cell phones are able, in good lighting conditions, to shoot good pictures, and they have sensors well above 10 megapixels.
And now, speaking of IR cameras, how many pixels does an IR camera have?
Very few…almost nothing compared to a digital camera. Today, the average IR camera used by inspectors has between 0.036 megapixels and 0.3 megapixels. The powerful new FLIR T1K, for example, has about 0.75 megapixels.
Even if you could artificially improve the resolution with some software options, a lower number of pixels means a lower ability to see details, thus a lower ability to properly measure the radiation, thus a lower ability to calculate the right target temperature.
When you select an IR camera for a task, the detector size and the lens angle are fundamental, otherwise your diagnosis based on temperature measurement or thermal pattern anomaly will probably be wrong.
Also, being too far from a target will reduce your ability to detect small problems which can become big problems later on. This happens with high-end cameras as well. Then, being too far away can make your observation angle unsuitable for detecting an anomaly, especially in an electrical cabinet full of wires and components.
General images of a target, such as an electrical cabinet taken from a 2-meter distance, are good for the report cover only.
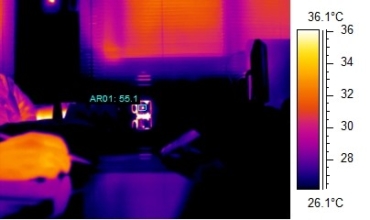
Cup with hot water measured at 1 meter and 5 meters with a high-end camera: the temperature drop between the two images was less than 2°C. The error is due to excessive distance in proportion to target size.
4)Not looking carefully at the “target face”
In your everyday life, you don’t go around checking the foreheads of your friends and family members for fever. You normally look at their faces first.
In thermography, a “good” face usually means the absence of problems, while a “strange” face means something is wrong.
Instead of looking only at the temperature reading (supposing that all parameters are set properly), look at the face of your component. A thermal map (the component’s IR face) that looks normal will probably indicate a component without problems.
An abnormal face, even if the abnormality is very small, can signal that something is going on. The ability to find this weak signal could make the difference between preventing damage and risking a dangerous problem in the near future.
5)Not being a master of thermal tuning and palette selection
What would you think if, during a medical checkup, the doctor told you that she was only able to find big problems? This is exactly what can happen if you don’t master thermal tuning.
Thermal tuning means manually adjusting the apparent temperature scale limits of your IR camera (the temperature scale on the right side of your image) to maximize the contrast on the target and highlight all small anomalies. In this case, even a delta T equivalent to 1K or less can be highlighted.
Useless? Wrong. The goal of an inspection is to detect an anomaly at the earliest possible moment, because the earlier the anomaly is detected, the greater the possibility that it can be easily solved.
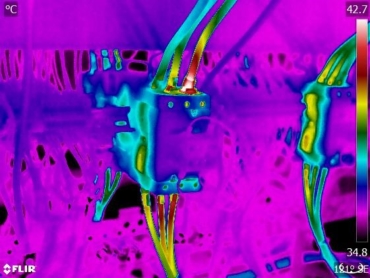
A good thermal tuning and a high-contrast palette can show you a loose connection at the earliest stage.
6)Ignoring higher-emissivity parts or being confused by different emissivity
Especially in industrial inspections, many materials can mislead you. Metals in particular, due to high reflectivity, show their surroundings better than themselves. This can result in cold parts appearing extremely hot or hot parts appearing extremely cold.
What if the hot part that appears cold is a connection of your most important electrical bus bar? You could be missing a hot or warm spot that may be a future critical point, placing your production under terrible risk.
To be on the safe side, look for high-emissivity parts like cable jackets, painted parts, stickers, and dirty parts. Maintenance folks should keep all components clean and shiny, but in some cases a bit of dirt can be your best friend. Even if you cannot measure properly, you will still be able to see an anomaly.
And be careful: similar components with different emissivity can mislead you as well!
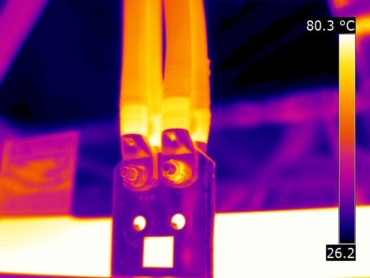
A low-emissivity aluminum bus bar appears to be cold and a bolt with higher emissivity appears to be warm: nothing wrong here.
7)Improper focus
A good optical focus (a crisp and sharp image) is fundamental, and not just in making you look like a professional and competent inspector.
The wrong optical focus means that the radiation isn’t properly focused on the detector, therefore, the radiation quantity detection and the consequent temperature calculation will be wrong—less than the actual temperature. An unfocused image means, then, a high possibility that you will miss minor anomalies and underestimate major anomalies.
8)Using the wrong detector type
IR cameras have different detectors. Be sure to use the right one for your application.
If you are a furnace or optical gas inspector you should know what to do, but unexperienced inspectors often accept challenges for which they are not perfectly prepared, and they could make the mistake of using their Long Wave camera to inspect something that requires a Middle Wave camera.
Crazy? Wait until one of your colleagues tells you the story of a technician that melted his brand-new Long Wave camera in front of a furnace inspection door during a tentative tube inspection that required a Middle Wave camera.
Or when one of your Level 1 students asks you, one year after certification, if it is possible to see a natural gas leak with a camera not suited for the job (and you wonder when you said something wrong during the classroom training…).
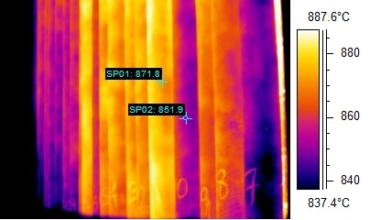
Image of tubes in a furnace: this inspection requires a Middle Wave camera to see through flames.
9)Not being curious
Yes, curiosity killed the cat. But sometimes curiosity helps you find something unusual or unexpected, or not planned for.
Therefore, when you are waiting for the department electrician or the maintenance manager, always look around. I have found so many issues by chance, just because I was curious enough to point my IR camera at different machines.
But if there are restrictions, don’t risk going to jail or getting hurt…because curiosity does sometimes kill the cat!
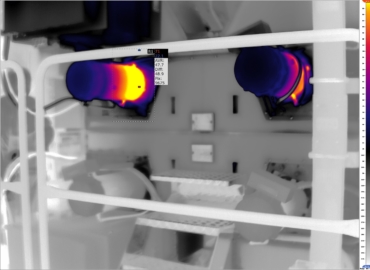
Found by chance: four water-cooled motors. The upper motors risk missing a coolant flow due to a valve failure.
10)Not knowing what to do
Yes, it seems obvious.
Sometimes, just because you have some competence with infrared, you are tempted to inspect something completely new or for which you lack experience.
Nothing wrong with that: every expert has done it in his or her career. Sometimes it is important to test yourself with new challenges or in areas where your competition has already failed. But this is only advisable with perfect preparation and planning.
Therefore, keep your brain busy: learn and learn. Never stop thinking of ways to improve your procedures and planning.