Have you ever completed an infrared survey and wondered if you’ve missed something that should have been inspected? Do you know the special safety instructions to open certain electrical cabinets? Do you have some information or thoughts that you want to keep for future inspections and don’t know where to keep that information? Has management ever asked you when was the last time that you’ve inspected a specific cabinet and you couldn’t answer them? Have you ever wondered if the cabinet that you’re about to open is the one that accidentally caused issues with another piece of equipment during the last inspection? If you have answered yes to any of these questions, you need to develop a check sheet for the equipment that you inspect. Check sheets are very important to use for many different reasons, but most of all for our safety.
Here at Cummins, Jamestown Engine Plant, we need to be sure that we are inspecting every cabinet, MCC, etc. every time that we go out for that specific area’s inspection. To make sure that we’re doing this in the safest way possible, we have created a safety check sheet. These sheets are maintained by our team. They are printed and reviewed prior to each inspection. The check sheets are a complete list of exactly which assets we need to inspect, the line in which they are located on and the nearest column number. They also contain important details or safety concerns, if any, for each piece of equipment that we need to review prior to opening the electrical cabinets. This will include any safety notes for the surrounding area that we need to be mindful of. This ensures that no matter who is suited up to perform the infrared inspections we all know what we need to inspect and any specific details regarding the equipment. Below are two examples of the check sheets that we use (some information has been removed due to security issues).
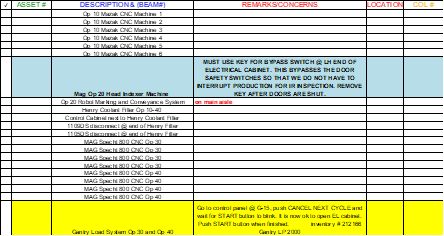
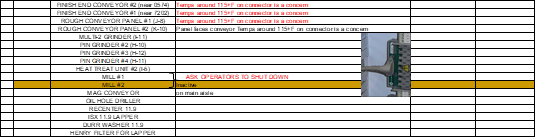
After printing the check sheets, we do a quick review of any safety precautions that are listed and make sure we have any special tools that we may need. The date of the inspection gets written at the top of the sheets so that we have that information for our history. We then suit up in our flame resistance gear and head out to the area that we will be inspecting. While performing infrared inspections, we always work in teams of two for safety reasons and our inspections are completely non-contact. There are two roles for this work. One person has the clipboard with the check sheet and the find sheets for writing down all the pertinent information if an anomaly is found. This person is responsible for following the procedure for safely opening the cabinets and maintaining a safe inspection environment while the thermographer is performing the scan. The second person is the thermographer and has the infrared camera. This person is responsible for maintaining a safe work environment while the first is opening the cabinet and is also the one who performs the infrared inspection. We rotate these roles so that we don’t get stagnant in our work and so that we can maintain our certifications.
Prior to opening any cabinet, we will note the asset number on the equipment and refer to our check sheet. We then mark off the asset to state that we have inspected it. We then review any remarks or concerns that we have noted from previous inspections. If there aren’t any, we follow our procedure for safely opening the electrical cabinets and the thermographer will perform an infrared inspection of the components within. Once the inspection is complete, all doors will be closed and any notes that are needed for future inspections will be added to our sheet. If we have a find within the cabinet, we write down all pertinent information for that anomaly on our find sheet. When we finish the inspections for the day, we write a report for each of the findings and then issue a work order for each within our Computerized Maintenance Management System (CMMS). Below is an example of a report and a work order (some information has been removed due to security issues).
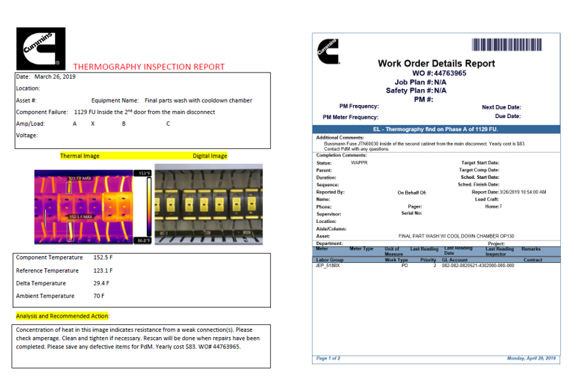
Once the reporting and work orders are done, we will then modify the check sheet so those remarks or concerns noted during the inspection can be viewed for future inspections. We save these sheets indefinitely as these reflect what assets had infrared (IR) findings at the time, which assets were locked out and could not be inspected, etc.
There are times during our normal inspection that we find out that a new piece of equipment is being installed. At this point if it is safe to do so, we write down all pertaining information regarding this new equipment so that it can be added to our check sheet. We also notify our CMMS group so that they can gather information from the engineers so that Preventative Maintenance (PMs) can be added for the equipment as needed. This group is responsible for ensuring that all new assets are listed within our CMMS so that PMs, work orders, downtime, and trades time can be captured, tracked and evaluated against each asset and like assets.
We have a very robust infrared program here at JEP. Our three-person Predictive Maintenance (PdM) Team has over 500 infrared PMs to complete at various frequencies throughout the year on our 1 million square foot facility. We record images of the cam gears after they’ve been heated in the assembly ovens prior to being installed on the engines to trend for engineering purposes. We inspect the battery chargers for the fork trucks throughout the facility for worn and/or loose connections. We inspect all main electrical cabinets, MCCs, IT server room, busways and buss plugs across the facility. We also have PMs that have us inspecting all substations via IR windows, the low sloped roof system, a summertime audit for A/C loss and a wintertime audit for heat loss. We need to keep track of what equipment we inspect and when the inspection has occurred. Check sheets are used for all inspections.
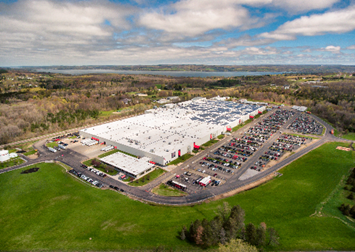
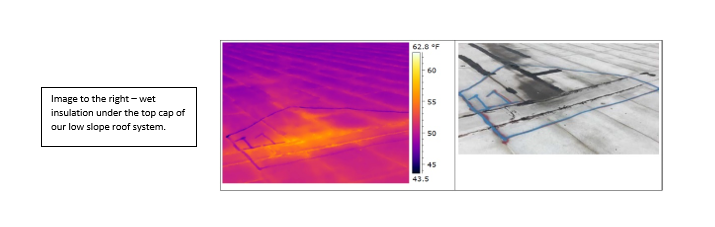
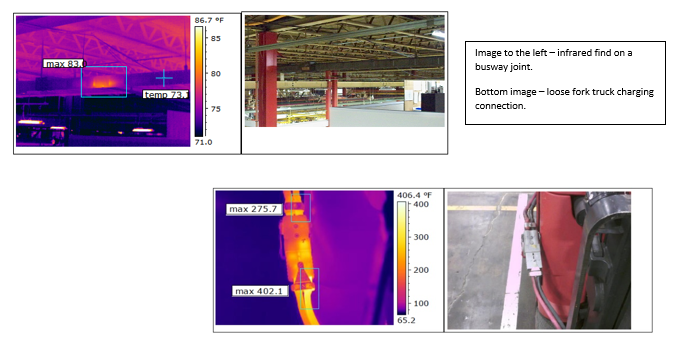
The check sheets have become an invaluable tool that we have used throughout the years. It’s not just to ensure that we’re inspecting the equipment that we should be, it’s an add on to the procedures that we have in place to ensure that we are safely opening the cabinets. We need to protect ourselves from any impending issues that may have been forgotten since the last inspection as well as eliminate any unnecessary downtime because we didn’t follow a specific step prior to opening the cabinet. Do yourselves a favor and develop a check sheet. You’ll save yourselves valuable time by being more organized and you’ll save the company money by avoiding unnecessary downtime by following the notes that are on the check sheets. More importantly, you’ll be able to go home safely after a hard day at work.