About the Author
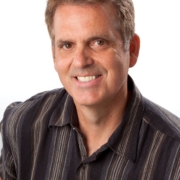
Brian Shanovich
Midwest Sales Manager, ACOEM
Brian Shanovich has over 26 years’ experience in reliability and proactive maintenance, including infrared and ultrasonic technologies, as well as vibration analysis and both geometric and shaft alignments. His specializes in the industries of pulp and paper, wind energy, and general machinery.
sir, when we take he speed of the gear wheel if the gear box is 5 reduction stage gear how we can set F-Max for 2 to 5 gear. For first gear speed will be the motor speed but from second gear should we consider the same motor speed of should take the rpm of particular gear.
thanks
Good morning Dorji. The short video clip you are referencing is correct in its statements concerning the calculation of Fmax. However, if you are using one of our systems (Hawk, Falcon, or SMC) the criteria for setting this “Frequency Maximum” is different. As was stated in the video the “rule of thumb” for setting Fmax is 70 times run speed of a motor. The reason for this is two-fold when manually analyzing the data. First, since bearing defect frequencies are different for each bearing type and number, based on their geometric construction, we need to assure enough defect frequencies are… Read more »
It is important to note, while 70x may be a general rule of thumb for most machines, it may not be sufficient FMAX in some applications. Consideration should first be made for the location of the bearing frequencies and your FMAX should be set at a multiple order of the highest expected frequency which is typically BPFI. A better rule of thumb would be a minimum of 10x BPFI with enough lines of resolution to resolve the lowest frequency of interest, typically FTF or cage frequency. I recently had a case on a roll where running speed was 400 RPM.… Read more »