It is always a challenge in the field of condition monitoring to monitor the machines which are not approachable, and that makes them prone to frequent failures. One of the similar equipment is the Air Handling Unit blowers in the industry. AHU blowers maintain the required temperature of the instrument panels, Battery room, UPS room, control room, etc. In case the AHU unit fails, the temperature of all the above-listed rooms will rise & subsequently affect the lifespan of the batteries, UPS, malfunction of panels etc. Because AHU blower is inside an enclosure, space constraint inside & draft from the fan makes it difficult to monitor the blower, which classifies it into a not-approachable but a critical machine.
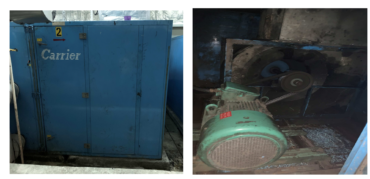
There was a catastrophic failure in one of the AHU blowers in the plant which pulled our attention to look for a solution on how to monitor the AHU blowers. We can remove the belt from the pulley & can check motor vibrations in a solo run, but this will state us only the health condition of the motor, the blower status is still unidentified. So we looked for wireless products in the market & choose a sensor i-Alert2, which was capable of measuring the vibration & temperature & displays FFT, Time waveform & trend plot on your mobile screen when connected through Bluetooth to the mobile phone.
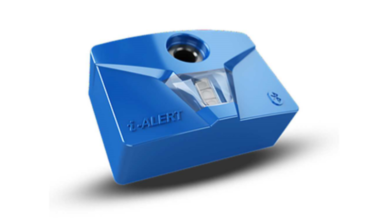
One of the AHU blower was identified & during the PM activity the wireless sensor was permanently mounted on its DE & NDE bearing housing.
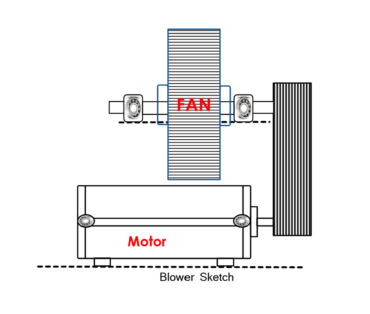
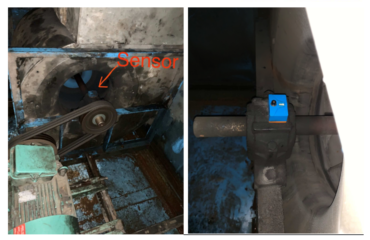
Blower details
Type – Centrifugal blower
Orientation – Simply supported
Blower RPM – 1450
Motor RPM – 1450
Transmission type – Belt Pulley
Blower bearings – DE & NDE 1311 EKTN9 C3
Motor bearings – DE 6312 C3, NDE 6212 C3
Observations
The max vibrations recorded were 71.3 mm/s for the fan.
FFT showed dominance of blower running speed with non-synchronous peaks at NDE bearing. However the phase measurement cannot be taken due to device limitation, it was planned to replace the NDE bearing, and balance the impeller.
Corrective action
• June-19 Fan bearings were replaced & impeller was cleaned, vibrations dropped to 30 mm/s • Oct-19 Impeller was balanced in the TAM, vibrations dropped to 6 mm/s
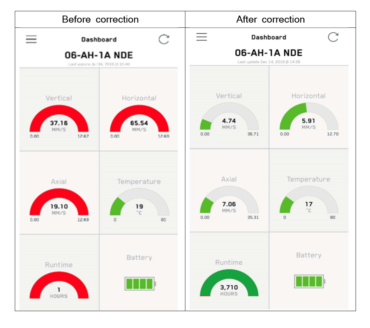
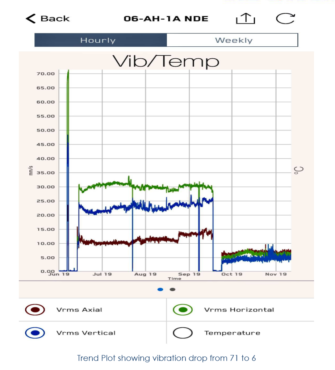
Looking to the effective application of these wireless sensors, we are installing them on all the AHU blowers across the plant & even looking to use them in other similar not-approachable equipment.
Nice Article Akil.
Thanks Mark
Very Innovative solution. If you are determined to bring results, nothing can stop you. This is the best examples.
How much would that sensor & application costs?
Hi Chiranjeevi
Thanks for the good words.
This one costs around $300, there are so many companies now with this type of product
Nice Material
Thanks Oliver
Thanks for sharing such great ideas. An innovative approach for accessing the remote points with wireless sensor.