Induction Motor Rotor Dynamic Balancing Case Study
Note: Picture from our Dynamic Balancing Jobs Database, not the case study rotor
This document is intended to provide a brief explanation of how electric motor acceptance vibration analysis tests combined with dynamic balancing jobs increase the life expectancy of rotating machinery.
On this occasion a rewinding job was executed by a local service company on a 3000 hp induction motor. After evaluating the machinery, the CBM team recommended that a dynamic balancing job was needed to reduce vibration levels to optimum condition. This document discusses the failure patterns related to an unbalance condition, key aspects to determine that the balancing job was necessary in order to meet our technical specifications.
Let´s Talk Reliability…
According to RCM (reliability centered maintenance) philosophy, maintenance activities should focus on ensuring that systems continue performing as required by the user in their present operating context. In other words, maintenance strategies should be designed after a minutious understanding of how machines fail and how we could prevent it from happening. A successful application of this methodology provides better risk management, cost-effectiveness, reliability, availability and maintainability of systems.
Following this principle, before establishing a maintenance strategy, it is essential to understand the work of Nowlan and Heap in determining how systems failed. In figure 1, the distribution of failure patterns is displayed. This will be discussed shortly.
Figure 1. Distribution of failure patterns according to Nowlan and Heap
It is important to notice the following from the Nowlan and Heap RCM study:
- Less than 20% of all failures are time based, which means that after a given period of time the probability of failure increases. Failures with this pattern are associated with preventive maintenance strategies.
- More than 80% of all failures have a random probability of occurrence. This is the main reason why nowadays condition-based maintenance is widely spread in all industries, since in most cases the probability of failures remains constant throughout the operation of the system.
- Around 68% of all failures have an infant mortality pattern, which means that it has a high probability of failure when a system begins its operation and afterwards proactive maintenance activities are suited for this pattern.
It is clear by now that QA/QC in the maintenance activities of rotating machinery is vital for cost efficiency when designing a maintenance strategy. In this case study, a no-load test was performed to a induction motor and a rotor unbalance condition was identified. In some cases a residual unbalance might be acceptable, but it is important to note that the life of the machine will be reduced significantly.
Diagnosing an Unbalance Condition
As mentioned before, an acceptance test was performed to a 3000 hp induction motor after a rewinding job was performed, and a condition of unbalance was identified. First, high overall readings indicate an abnormal condition, as shown below. Since the high amplitude occurs only in the vertical direction in both motor bearings, a resonance condition was also considered.
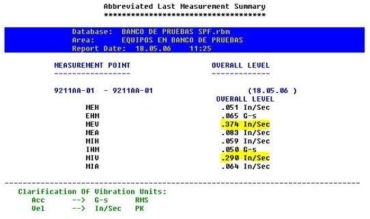
Afterwards, further details are obtained from the vibration spectrum. In Figure 2, the vibration spectra before and after the execution of the balancing job are shown. It is important to notice high vibration amplitude at the motor’s running speed. At this point, there is not enough information to correctly determine the maintenance recommendation activity.
Figure 2. Comparison of vibration spectrum before and after the execution of the balancing job
Finally a coast down test was performed after the motor was turned off. Even though the coast down was performed after the motor had lost some speed, it is sufficient to note that unbalance is the abnormal condition. The most important characteristic to note is that unbalance could be interpreted as the centrifugal force produced by an equivalent residual weight at a given radius; as indicated by the below equation, the high vibration amplitudes are in some degree proportional to the square of the running speed of the rotor. In Figure 3, the coast down test shows that the vibration amplitude decreased as the speed of the machined decreased. If the high vibration amplitude had a sudden descent after it moved off a +/-15% range from the running speed, there is a high probability that there is a resonance issue.
(Equation 1)
Figure 3.- Coast Down test performed to the motor
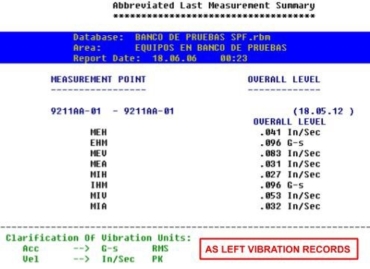