About the Author
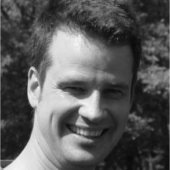
Kris has expertise in vibration analysis and industry experience in all major industries, including chemicals, automotive, power, gas and food & beverage.
READ FULL BIOTo improve safety and keep up the production time, ArcelorMittal asked us to investigate possibilities to perform wireless monitoring on their cranes.
Compared to most applications, wireless monitoring of overhead cranes is quite challenging. We need high-speed sampling for fault detection. And because this is a low-speed application, we need at least 20 seconds to get a time waveform. We need a trigger to start the measurements because it’s a discontinuous process. And Arcelor wanted it to be wireless. The electrical cabinet of the crane is in the beam, and there would have to be a lot of long cables if the system was not wireless. It’s also hard to manage cables in the trolley.
Although many wireless vibration systems are available, none of the existing systems we investigated could fulfill all of the requirements, even our own Wi-care 100 system. It has high-frequency samples and the ability to send raw and wireless data, but it lacks the trigger and is battery operated.
We presented our new Wi-care 200 series, still under development, to Arcelor because we thought they fit the requirements: high-speed sampling, smart data capturing on external trigger, and local power supply. And we performed a test with it. The Wi-care 200 did get a clear reading of a bearing fault and gave us a clear spectrum at 40 RPM.
When we added the bearing defect frequency, we saw that it was the outer ring of a 22/236 bearing, all measured while the system was in production.
We have three main hardware systems: the sensors, the Wi-care 200 series, and the gateway. With the Wi-care 200 we are reading data from the sensors and transmitting it to the gateway wirelessly. The gateway gathers all the information from all the Wi-care units, transmits it, and reads out the process data, such as speed of the crane and trolley, position of the crane and trolley, speed and position of the hoisting. This is sent to the Wi-care system, which is triggered to start the measurement.
We can also save the process data in our measurements. When you want a trend line of a crane speed, for example, you can select it and filter out the other measurements.
Arcelor asked us to set up the system on the same crane we’d conducted our first measurements on, several years before. The sensors are placed close to the asset, so there is a limited cable way. In this case, cables were installed between 1 m and 5 m. In this case, the data is being transmitted to the drive of the crane. We installed the gateway so the data was sent wirelessly.
Wi-care 200’s flexible two-way communication also allows easy integration of other technologies and sensors: temperature, online oil analysis, thickness, etc. The client wanted some other sensors, so they installed ultrasonic distance sensors, and we read them out. Normally, each sensor has its own software, but we can read all the sensors in our system and send the data out in one platform.
One advantage is that the cable lengths remain very local. This is the complete wireless system we installed:
· 97 sensors
o 50 vibration sensors
o 21 online oil sensors (oil quality, oil wear, oil level)
o 26 ultrasonic distance sensors (thickness of brake liner, hoist cable, carbon brushes)
Thickness measurements are transmitted with the same wireless system, and results are available in the same analysis software.
In conclusion, the wireless Wi-care 200 system further increases the reliability of our crane monitoring program while eliminating the disadvantages of the existing (successful) periodic program.
Kris has expertise in vibration analysis and industry experience in all major industries, including chemicals, automotive, power, gas and food & beverage.
READ FULL BIO