Motor acceptance testing is a critical part of many preventive maintenance programs and can be key to catching electrical problems before they cause considerable downtime. With more than 35 years of motor testing experience ALL TEST PRO® has determined that 25 to 30% of new or newly rebuilt motors can exhibit a fault. Not all bad motors result in considerable downtime, but these faults may reduce motor efficiency and create additional and repetitive maintenance. MCA™ allows users to stay productive, avoid expensive replacements and minimize damage to critical motors. But what exactly is acceptance testing, and how do you know when to accept or condemn a motor? We’ll go through the basics in this overview of motor acceptance testing, along with the types of equipment you can use for testing.
What Is Acceptance Testing?
Inspection and acceptance testing is done using Motor Circuit Analysis (MCA™), a series of non-destructive, deenergized tests that provide a comprehensive picture of the motor’s electrical health.
The tools that most technicians use every day to assess the electrical health of motors is rooted in last century technology. The Tools may have modern user interfaces, but their capability to analyze the health of the electric motor has not progressed beyond what was used in the 1970’s. The common names for these tools include the meg-ohm meter (megohmmeter) for evaluating the condition of the insulation system between phase and ground, and the digital multimeter (DMM) which is used to measure phase to phase resistance. The main purpose of an Insulation Resistance to Ground Test with a Meg-ohm meter is to evaluate if a motor is safe to run or not. By performing an Insulation to Ground test, only insulation system between the windings of the motor and the frame of the motor or ground are tested. Many people think if the motor passes these tests, then the motor is fully functional. But what if the insulation is starting to degrade between two conductors internally in the winding system? If the insulation has not fully been compromised and there is no direct short between two wires, two coils, or two phases of the winding system then a standard digital multimeter will not detect a change of resistance and this developing fault will go undetected until a critical failure occurs. Also, by implementing incoming inspections rotor faults can be detected such as fractured rotor bars or casting voids that occur during manufacturing. Typically, these faults are not able to be seen by eye so without proper testing these faulty motors will be put into service only to fail in a short period of time.
Acceptance testing is a very important part of any electrical reliability program. Incoming inspections evaluates the condition of the motor before it is accepted by the plant while it is still covered by warranty, ensures the motors in storage are in good condition and capable of providing long term trouble free operation. The patented Dynamic test thoroughly evaluates the winding, rotor, and ground wall insulation system and confirms the motor is in a good condition. The Static test creates a single number called Test Value Static (TVS) that defines the condition of the motor at that point. The TVS value is established by placing all of the acquired measurements into a proprietary algorithm that results in a single value. This value will stick with the motor from the first time a test is performed until the motor finally fails and needs to be replaced or rebuilt. Any changes in this number compared to a baseline test indicates a developing fault in the rotor or winding system. Electric motor acceptance testing is performed on the windings of a three-phase electric motor to assess those components. The instrument automatically tests each coil individually and then compares the values for any imbalances in resistance, impedance, inductance, phase angles and current frequency responses.
The static test and dynamic test should be performed to establish a baseline test result before installing any new motor. This baseline comes from the Test Value Static (TVS), a number that only comes from ALL-TEST Pro tools and is calculated from a three-phase MCA™ static test gathered from equipment like the ALL-TEST PRO 7™ or the ALL-TEST PRO 34™. These tools are handheld and battery-operated, making them excellent for fieldwork. They carry a range of data analysis and storage features. There is no need to move test leads. The instrument instructions are on the screen. Test takes about 3 minutes to perform.
GET A QUOTE
Motor acceptance testing is a key component of a successful preventive maintenance program, revealing critical information about a motor’s health and providing early identification when issues start to appear. These tests can help you avoid downtime, safety issues, and keep your equipment moving.
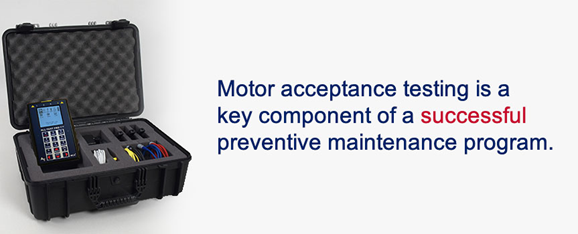
Factors to Consider When Accepting a Motor
When testing and ultimately accepting a motor, you must factor motor criticality, type of faults, and location of the motor.
Motor Criticality
Critical motors generally require stricter acceptance criteria. Because motor errors in critical areas have more significant ramifications, higher tolerances should be used to determine suitability. A motor in a highly critical part of a production line might be condemned for a small variation in phase angle or current frequency response, while that same variation in a less important area may not be cause for concern. These non-critical locations have more room for risk in terms of operational effects.
The phase angle and current frequency response tests are the most sensitive tests for detecting developing turn-to-turn, coil-to-coil, and phase-to-phase shorts that standard ohm meters and meggers can’t detect. Other factors that may vary by criticality include WARN or BAD statuses on a dynamic test. These results could cause a user to condemn a motor where unexpected downtime is unacceptable. Many facilities use their scheduled downtime to replace or fix these motors.
Users can perform these tests with the ALL-TEST PRO 7™, the ALL-TEST PRO 7 PROFESSIONAL™ or the ALL-TEST PRO 34™. Each of these devices features easy-to-use interfaces and a range of testing capabilities, making them suitable for many tasks across your preventive maintenance plan.
For a less critical motor, poor readings for phase angle, variation frequency or dynamic testing may be acceptable, as downtime for this equipment is not detrimental to the operation and motor and labor costs are significantly lower when running to failure.
Type and Location of Fault
You’ll also want to consider where the fault is located and what type it is:
- Winding shorts: A winding short is typically more critical than contamination or rotor faults. Determine the condition of the windings by evaluating the TVS and any imbalances in phase angle and current frequency response. If the motor windings test is good, the cable likely has a fault. If the test improves but still has a fault, there is likely an issue with both the cable and winding. Lastly, if the test has the same results at the motor, the stator windings have the fault. Internal winding faults are typically a sign of failure for the motor.
- Inductance or impedance unbalance: Motors with either of these issues should be evaluated next. Perform a rotor reposition test or rotor compensation test to determine if the fault was caused by a faulty rotor or by the rotor bar to winding ratio. Three-phase AC induction squirrel cage motors of less than 1,000 volts should also receive a dynamic test.
- Size of unbalance: Motors with small resistance unbalances alone generally have the lowest condemning priority.
- Location: Depending on where the fault is located — such as the cable or motor winding — you’ll want to adjust priority accordingly. The same reasoning applies with hard-to-reach motors such as overhead cranes, fans, and submerged motors.
Getting the Right Supplies with ALL-TEST Pro
Testing of new and rebuilt motors is an essential step in a proactive motor management philosophy. To do it, you need the right tools. At ALL-TEST Pro, we create a variety of products designed to deliver unique insights into the health of your equipment. Our goal is to help you eliminate unplanned downtime and save you money by preventing safety issues & expenses related to motor repair, downtime, & production wastes & disposal, that may occur from an unsatisfactory installed motor that is meant to keep your processes operating efficiently.