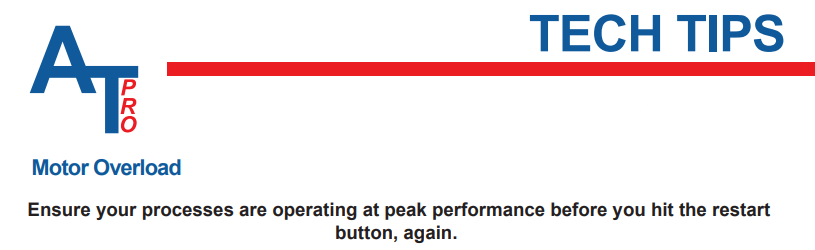
Motor overloads occur when motors are drawing too much current. The main issue with excess current is that it creates heat which degrades the insulation surrounding the conductors that creates stator magnetic field. Continued degradation of the winding insulation results in failure of the insulation and eventual motor failure.
It is important to recognize that an overload condition exists but just as important to determine and correct the cause of the overload before attempting to restart the tripped motor.
There are many reasons why motors draw excess current, but they can be classified as mechanical, electrical or load related.
Mechanical issues include (but are not limited to) mass unbalance, shaft or bearing misalignment, over-tighten or loose belts. These faults are the most common sources of vibration associated with rotating equipment. Approximately 30% of the time, when these sources are
present, they will create a resonant condition. Resonance occurs when the frequency of an oscillating force is near the natural frequency of a spring system. Resonance is an enormous energy robber and will create an increased load to the motor.
Electrical issues can be a cause of incoming power, such as voltage mismatch, (over voltage or under-voltage), voltage unbalance or excessive harmonic content. Winding insulation degradation or breakdown can cause intermittent faults. Since electrical insulation has a negative temperature coefficient, these faults disappear after the motor stops and the insulation cools. Electrical Rotor issues such as static or dynamic eccentricity, cracked, broken rotor bars or casting voids cause the rotor to operate below rated speed which reduces the back emf created by the rotors turning action and will cause an increase in rotor current.
Process or load issues such as too much flow, cavitation, flow resonance will also cause the rotor to run below the rated speed which causes the motor’s rotor current to increase, creating an overload condition.
To protect against these failures, motor controllers have protective relays (overloads) that automatically remove power from the motor to prevent these failures from causing the motor to catastrophically fail. In most applications the motor trip is the first indication of a problem in the motor system.
When this occurs, operators are allowed to attempt to restart the motor 3 times before contacting maintenance. However, depending on the cause of the overload, these restarts may be exacerbating the issue resulting in further motor damage or catastrophic failure. Restarting the motor does not address the cause of the excess current.
ALL-TEST PRO 7™ provides an easy-to-use handheld instrument that can provide you with a complete and thorough examination of the motor system from the Motor Control Center (MCC) in less than 3 minutes. These tests ensure the motor is “safe” to restart. This instrument will quickly evaluate the condition of the ground-wall insulation, winding insulation, and any developing rotor issues and assesses the condition of the motor and displays its condition on the instrument screen in one of three conditions, “Good”, “Warn”, or “Bad”.
After the motor is restarted or even before the motor trips the ATPOL III™ can be used to evaluate the entire motor system from incoming power to the entire process itself. The ATPOL III™ uses the motor’s voltage and current to completely analyze the entire motor system while the motor is operating under load. The ATPOL III™ performs a simultaneous data capture of all three phases of voltage and current to quickly evaluate any power supply issues that can cause the motors current to increase. Additionally, it performs an A/D conversion of the motor’s voltage and current that is uploaded to the ESA Software to evaluate the electrical and mechanical condition of the motor as well as the mechanical condition of the driven machine.
After resetting the overloads, the operator will restart the motor. If the motor operates successfully, that is usually the end of the situation. However, the reason the motor tripped is still unknown and it could cause additional trips to occur in the future. Typically, each subsequent trip occurs at reduced intervals indicating further degradation of the motors condition. However, before restarting the motor, a few basic mechanical and electrical checks should be performed.
Recommended procedures to an unexpected motor trip or the most basic checks performed before attempting to restart tripped motors:
• Mechanical check is to rotate the shaft: Does the coupled shaft rotate freely?
If not, determine if it is the motor or the driven machine that is preventing the motor system shaft from rotating freely, by separating the coupling and turning each of the machine’s rotating element. If either shaft does not rotate, correct the fault prior to attempting a restart. If either of the machines does not rotate freely suspect the bearing.
• Electrical checks
Use the ALL-TEST PRO 7™ to perform all the static tests and Insulation Resistance to ground (IRG) tests from the MCC. If a fault is detected from the MCC, retest directly at the motor. At the motor perform the static test, IRG, dissipation factor (DF) and capacitance to ground. If the Test Value Static (TVS) deviates by more than 5% from Reference Value Static (RVS) perform a Dynamic test. If the TVS is <3% from average and DF & IRG are within recommended range the fault is in the cabling or the controller.
After restarting the motor, conduct an energized test using the ATPOL III™ to evaluate the mechanical and electrical condition of the entire motor system. These one-minute tests will determine the quality of the incoming power, the electrical and mechanical condition of the motor, the mechanical condition of the driven machines as well as any anomalies of the process such as cavitation, pump impeller clearance issues or flow resonance.
The ESA Software then automatically analyzes the uploaded test results to evaluate and report the condition of the entire motor system in an easy-to-understand multi-page report that provides the electrical and mechanical condition of the motor and the driven machine.
