Today, there is a new generation of CMS devices that overcomes the barriers that have traditionally prevented an adequate condition monitoring service on critical rotating machinery. The use of these new CMS, in combination with the usually pre-installed Machine Protection Systems (MPS), requires a proportionally small investment but provides numerous advantages that increase the reliability of those assets.
Machinery Protection Systems (MPS) are quite common on critical rotating equipment.
The critical machines are characterized by high initial capital investments and a high impact on production in case of unplanned downtime. Maintenance operations involve high costs and some of the components may be difficult to replace or manage. They are high-power machines, usually with shafts supported on plain bearings. These types of machines are common in the chemical, petrochemical, and power generation industries, as well as in other industries: paper mills, water treatment plants, cement plants, steel mills, manufacturing plants, mining sector, etc. These include gas and steam turbines, compressors, electric motors, blowers, fans, gearboxes, etc.
These critical assets are typically supplied with an integrated protection system, which includes both the acquisition hardware and its associated sensors, forming part of the instrumentation since the commissioning.
The instrumentation typically includes displacement probes for monitoring relative shaft vibration and axial displacement, as well as housing mounted seismic sensors (absolute vibration) and a keyphasor for rotational speed and phase reference measurement. These units are already instrumented with permanently installed vibration sensors.
Such sensors are also suitable for Condition Monitoring Systems (CMS). Many protection systems include or can be upgraded to incorporate condition monitoring capabilities. Many users, however, do not take advantage of the capabilities offered by this valuable instrumentation installed on their machines. There are several reasons for this:
- Upgrade costs. The cost of upgrading an MPS to incorporate Condition Monitoring capabilities (including firmware, server, databases, software) is usually high.
- IT-related difficulties. Upgrading protection systems to incorporate Condition Monitoring capabilities often involves the installation of network infrastructure and changes in system architecture, which require the intervention of the IT department (interconnecting networks, overcoming security problems, installing servers and databases, establishing maintenance plans, etc.).
- Specialized personnel. The analysis and diagnosis of this type of machine requires highly specialized personnel.
- Low failure rate. This critical equipment normally has a low failure rate, which together with the protection system itself, does not contribute to the implementation of Condition Monitoring systems, creating the false impression that they are not necessary.
As a result of all this, paradoxically, much critical machinery is not routinely included in plant predictive maintenance programs, so it is not properly analyzed and diagnosed.
This means foregoing the benefits of Condition Monitoring systems on precisely those pieces of equipment that are most critical. These benefits include:
- Reduced downtime. Protection systems can prevent catastrophic failures, but they do not prevent unforeseen failures with the consequent loss of production.
- Lower maintenance costs. Condition Monitoring systems provide information on the health status of machines and detect incipient failures. This allows for minor and planned interventions, reducing maintenance costs.
- Increased reliability and service life. An early maintenance intervention, when the failure is incipient, avoids catastrophic failures, increasing the useful life of the machinery.
- Increased safety. Early detection of faults increases operational safety and reduces the risks associated with failures and breakdowns.
Currently, there is a new generation of Condition Monitoring Systems (CMS) appearing in the market, which can help to overcome the difficulties exposed above.
First of all, they are low-cost equipment, although they include all the necessary tools for the analysis of critical machines: spectra and time shapes, spectrum cascades, orbits, Bode and Nyquist plots, shaft centerline, etc.
They are small in size and easy to install and maintain as they do not require an external server for data storage and visualization. The data are stored in the hardware itself, which includes a web interface, both for configuration and the visualization and diagnosis of the equipment.
They are usually connected to the buffered outputs of the MPS systems, allowing users to take advantage of the installed sensors to incorporate a high value-added Condition Monitoring system to their most critical assets at a very reasonable price.
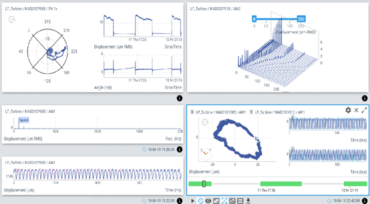
Fig 1. Modern CMS graphical interface, fully customizable in small windows or widgets. This example shows the phase diagram, spectra cascade, trend, and orbit.
As part of the features of this new generation of CMS systems, it is worth highlighting their open architecture and communication protocols. These new CMSs are optimized to work over LTE networks for remote access to their interface, with the use of a simple web browser and from any type of device or operating system. They also include a communications API, an FTP server for data export, bidirectional communication of static variables with control systems via Modbus-TCP and OPC-UA protocol, and a VPN client for secure remote connections. All this facilitates remote access to data by an expert analyst, who could be located anywhere in the world, thus eliminating the need for specialized personnel on the plant side.
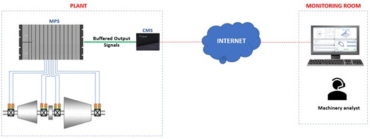
Fig 2. Scheme of turbomachinery monitored by existing MPS, to which a modern CMS is coupled, connected to the Internet for remote diagnosis and analysis by an expert.
Finally, the simplicity of the architecture of these CMSs makes it possible to avoid typical difficulties with IT departments, barriers that are often difficult to overcome in some organizations. These CMSs are completely autonomous and do not require external servers or other IT infrastructure. Users can access the system, and all stored data, with a simple web browser. Should the plant decide to outsource machinery diagnostics to external analysts, all that is required is to provide an Internet connection (using the plant network or an LTE connection). That way any analyst will be able to access the data, in real-time or historical, through a secure VPN connection. In those cases where connecting these CMSs to the Internet is not an option, these systems provide tools to extract data automatically and incrementally, which can then be sent to an external server to be analyzed by an expert using a virtual CMS with identical analysis and diagnostic tools.
In summary: A new generation of CMS equipment is now available to overcome the barriers that have traditionally prevented a proper Condition Monitoring service on critical rotating machinery. Its use in combination with the protection systems (MPS), which such machines usually have pre-installed, is a proportionally very small investment but it allows to obtain numerous advantages that favor the reliability of such assets.
Fascinating