Since January 14th, we increased the frequency of measurements on a guide roll bearing in a paper machine due to rising acceleration levels. We did not have online monitoring, so our condition-based approach was crucial in detecting early signs of failure. The roll was in a challenging location, hidden behind the frame, making maintenance complex. Replacing the roll also meant changing the wire, which was not yet at the end of its campaign.
The lubrication system used a rotameter, so as soon as we detected the first increase in acceleration values, we evaluated whether increasing the flow rate would be a valid action. However, the trend persisted, indicating that the issue was not related to lubrication alone.
The first warning came when acceleration reached 1.98 Gs, showing carpet delamination and peak deltas matching inner and outer race frequencies. The bearing in question was a CARB 2319 K C4. We continued tracking it until March 24th, when a sudden spike pushed acceleration to 3.24 Gs, entering a critical range where reliability could no longer be assured.
We extended operation until a planned shutdown on March 27th, when we decided to replace the entire roll—a better choice than changing just the bearings. Even though the wire had to be replaced, the savings from avoiding an unplanned failure justified the decision. The intervention was completed in 6 hours, while a functional failure could have caused 12 to 14 hours of unplanned downtime.
This was a great example of predictive maintenance preventing a major failure. Have you faced similar challenges without online monitoring? What were the root causes of failure in your experience? Here, we found misalignment, oxidation marks, excessive clearance, and significant housing damage. Let’s discuss—what would you have done in this situation? Drop a comment and share your insights!
Guide Roll 4II8
Context:
Monitoring began in January 2025 when the equipment condition shifted from normal to alert, indicating bearing wear. Due to the difficult access location—since the roll is positioned behind the chair—any intervention was more complex. In February, the condition escalated from alert to alarm, reinforcing the recommendation for bearing replacement. As an immediate action, we increased the flow rate of the rotameters and continued to monitor the asset more frequently until the intervention could be scheduled. Given the complexity of accessing the location, which required cutting the screen, and considering the elevated vibration values indicating a high risk of functional failure, the decision was made to replace the entire roll.
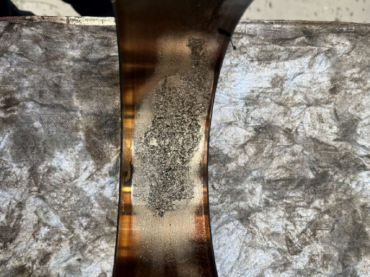
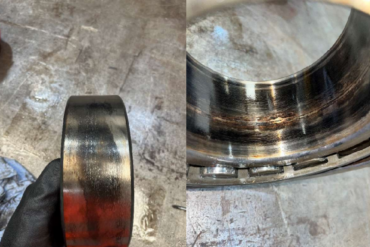
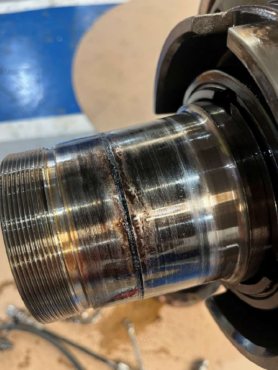
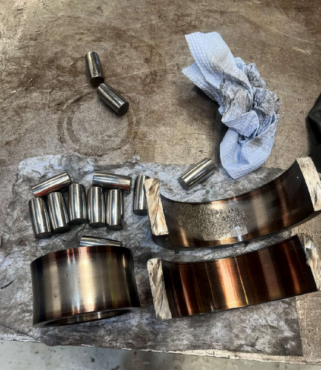
Action Taken:
An RDP (Predictive Diagnosis Report) was issued indicating the bearing housing, and the replacement of the roll was requested.
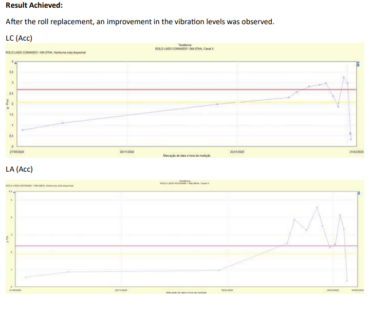
Comments:
Critical Failure Prevention:
Early defect identification was crucial in preventing more severe damage to the equipment, such as failure of the bearings, housings, shaft, or even the roll itself.
Operational Safety and Availability:
The intervention not only addressed the immediate issue but also ensured continued operation, preventing unexpected downtime and safeguarding the equipment assembly. Vibration analysis proved to be an essential tool for optimizing predictive maintenance and the operation of rotating machinery.
Scheduled Intervention:
Performing maintenance interventions during scheduled shutdowns is a key strategy in industrial maintenance, allowing for the correction of potential failures without compromising operational performance or causing unplanned downtimes. A functional failure of the assembly could have resulted in a complete machine stoppage.
Conclusion:
Vibration analysis proved to be an essential tool for the early detection of failures and for supporting strategic decision-making in the maintenance of critical equipment. The swift and efficient intervention not only prevented a catastrophic system failure but also generated significant cost savings, ensuring operational continuity and maintaining a safe production environment.