About the Author
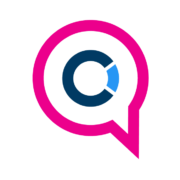
Pumps are critical pieces of equipment in a large variety of industrial settings. Although they are routinely monitored as part of a facility’s CBM program, the data captured in this way isn’t always enough to identify the signs of early-stage pump cavitation. While pump cavitation is easy to identify by the churning gravel noise, once you can hear it the pump is likely damaged. Proactively diagnosing and addressing the issue will save a lot of headache. Vibration data can provide valuable insight into the pump’s condition, and with the right monitoring setup can help you identify developing cavitation before serious damage or failure occurs.
Pump vibrations are generally between 450 – 300,000 CPM, including the drive motor harmonics; vane pass, gear mesh, and reciprocation impact frequencies; and some bearing faults. When cavitation begins to develop, the impacts of bursting air/vapor bubbles inside the pump create small shockwaves which wear down the impeller over time. These small impacts change the overall vibration level of the pump and produce increasingly high-frequency spikes in the time waveform, which can cause sensor overload and signal corruption. While 4-20mA sensors can detect these amplitude increases, it may not be realized in time and you’ll still need to perform the analysis to identify exactly what is causing the vibration. For this reason, IEPE accelerometers are recommended for frequency analysis to better identify the faults.
High frequency vibrations, from 300,000 – 650,000 CPM, are often present during the onset of cavitation. Other common pump faults, such as misalignment, imbalance and looseness, are generally mid-frequency faults, so intermittent high-frequency measurements can indicate that the problem is more likely to be cavitation. Entrained gas, high pressure leaks, and incipient bearing faults are also possibilities to consider if you’re seeing high frequency noise. If using a general purpose 100 mV/g accelerometer or a high sensitivity/low frequency sensor, these high frequency, high amplitude readings can distort the signal and overload the sensor. This will often appear as a clipped signal or ‘ski slope’ data and indicates that a lower sensitivity/higher frequency sensor is needed to capture the true vibration level of the pump.
For general purpose monitoring of pumps, a 100 mV/g general purpose accelerometer is usually adequate and should be an appropriate selection if the pump has never experienced a specific problem to look out for. If cavitation is of particular concern for a specific pump, or the time waveform has already shown signal corruption, it’s advisable to use a 10 mV/g sensor to better capture high frequencies. This is due to the fact that the lower sensitivity enables a higher dynamic range, meaning more vibration can be measured by the sensor before the output is saturated. Having a high-amplitude vibration signature, pump cavitation is a destructive condition and catching it early through vibration monitoring can help minimize the damage and downtime it can cause to industrial processes.